Professional packaging machine repair service for ensuring operational success.
Wiki Article
How Professional Product Packaging Device Repair Work Services Reduce Downtime and Boost Productivity
Specialist product packaging maker repair work services are crucial in decreasing downtime and boosting performance via specialized diagnostics and prompt treatments. The implications of such services prolong past immediate repairs-- unloading the wider effect on functional effectiveness discloses crucial insights into long-lasting productivity methods.Value of Timely Repairs
Prompt fixings of packaging makers are critical for maintaining operational performance in any type of manufacturing environment. When equipment malfunctions or breaks down, it can bring about substantial interruptions in manufacturing lines, leading to raised downtime and shed income. The longer a product packaging machine remains out of commission, the greater the effect on overall efficiency, possibly triggering hold-ups in meeting orders and lessening consumer contentment.In addition to the instant economic effects, postponed fixings can bring about more comprehensive damages to the equipment. Elements that are not dealt with quickly can weaken additionally, calling for more pricey fixings or complete replacements, which could have been prevented through prompt treatment. Normal maintenance and timely repair services can enhance the life expectancy of packaging makers, making certain that they operate at optimum performance levels.
Purchasing specialist product packaging equipment repair service services is crucial for reducing these threats. A proactive technique to repair services not only keeps manufacturing routines yet likewise cultivates a culture of dependability within the company. By prioritizing timely repair work, companies can keep their competitive side, enhance resource allotment, and ultimately enhance their bottom line via improved operational performance.
Competence in Diagnostics
When it comes to keeping the efficiency of packaging machines, experience in diagnostics plays a crucial duty in identifying concerns prior to they intensify into major failures. Knowledgeable professionals use advanced analysis tools and methods to carry out extensive evaluations of machine performance. This proactive approach enables them to determine the source of breakdowns, whether they originate from mechanical wear, electric faults, or software application inconsistencies.
Reliable diagnostics not just assist in quick identification of troubles however additionally improve the overall reliability of product packaging procedures. By conducting thorough analyses, professionals can examine the health of important elements, ensuring that also minor irregularities are attended to without delay. This interest to detail decreases the danger of unforeseen breakdowns, which can bring about expensive downtime.
Furthermore, expert diagnostics offer beneficial insights into functional trends, permitting businesses to make enlightened decisions regarding devices upgrades or modifications. By leveraging these insights, firms can enhance their product packaging processes, bring about enhanced efficiency and productivity. Inevitably, buying diagnostic know-how is essential for companies seeking to preserve smooth operations and maintain high standards of quality in their packaging procedures.
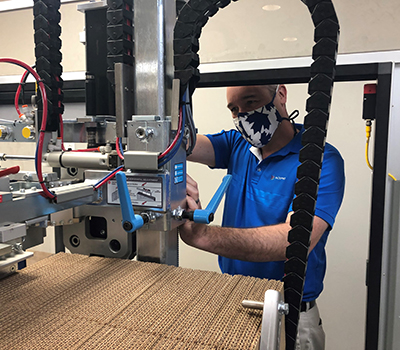
Preventive Maintenance Conveniences
Preventive maintenance matches professional diagnostics by proactively dealing with prospective concerns prior to they manifest into major troubles. By carrying out an organized preventative upkeep program, companies can dramatically minimize the danger of unanticipated equipment failings, thereby minimizing expensive downtime. Normal inspections, cleaning, and parts replacement help ensure that packaging machinery operates at optimal efficiency.One of the key benefits of precautionary maintenance is its ability to extend the life-span of equipment. By routinely maintaining machinery, businesses can avoid the intensifying results of damage that usually bring about significant repair services or substitutes. This not only saves capital yet additionally improves the overall dependability of production processes.
In addition, preventative upkeep adds to improved safety and security problems within the office. By recognizing and remedying potential hazards imp source before they escalate, companies produce a safer setting for their staff members (packaging machine repair service). This aggressive strategy not just safeguards employees however also promotes a society of responsibility and vigilance

Personalized Solution Solutions
Recognizing the distinct demands of each business, personalized solution solutions for packaging equipment repair deal tailored techniques that boost operational performance. These solutions are developed to attend to details challenges dealt with by different markets, making sure that equipment downtime is minimized and productivity important link is made the most of.Specialist repair work services begin with a detailed analysis of a firm's packaging procedures. By recognizing the details equipment included and the demands of the production setting, technicians can develop a personalized maintenance and repair strategy. This may consist of specialized training for internal personnel, the application of predictive maintenance technologies, or the arrangement of committed assistance throughout optimal manufacturing times.
Additionally, tailored remedies can incorporate flexible service arrangements that line up with a business's operational routine, permitting repair services to be carried out during off-peak hours. By focusing on the special demands of each service, these bespoke solutions make certain that repair services are not only effective but also seamlessly incorporate into existing operations.
Eventually, the concentrate on personalization makes it possible for business to optimize their product packaging processes, bring about improved integrity and efficiency of machinery, which is critical for keeping competitive benefit in today's fast-paced market.
Effect On General Efficiency
Personalized service options not just address certain fixing demands however additionally play a considerable role in improving total operational effectiveness. By giving targeted interventions, expert packaging check maker repair solutions straight reduce the frequency and period of equipment failures. This aggressive approach guarantees that production lines stay functional, minimizing interruptions that can bring about costly downtime.Additionally, effective fixing services add to smoother process, as properly maintained machinery operates at ideal performance levels. When devices work appropriately, the quality of packaged products enhances, leading to fewer flaws and much less rework. This improvement not just boosts productivity yet likewise enhances consumer satisfaction.
Furthermore, routine upkeep and fast reaction times from repair service specialists cultivate a society of dependability within the company. Employees can concentrate on their primary tasks rather than bothering with potential tools break downs. As a result, the overall throughput of the production process increases, allowing business to fulfill need a lot more successfully.
Eventually, the calculated investment in expert repair solutions converts to enhanced efficiency across all functional facets, making sure that companies can adapt and thrive in an open market. This harmony in between upkeep and performance is necessary for long-lasting success.
Conclusion
In final thought, specialist packaging maker repair work solutions play a vital function in decreasing downtime and enhancing efficiency within making settings. Prompt repair services, specialist diagnostics, and preventive maintenance contribute to the dependability of tools, while customized service remedies address particular functional demands.Report this wiki page